GMP System
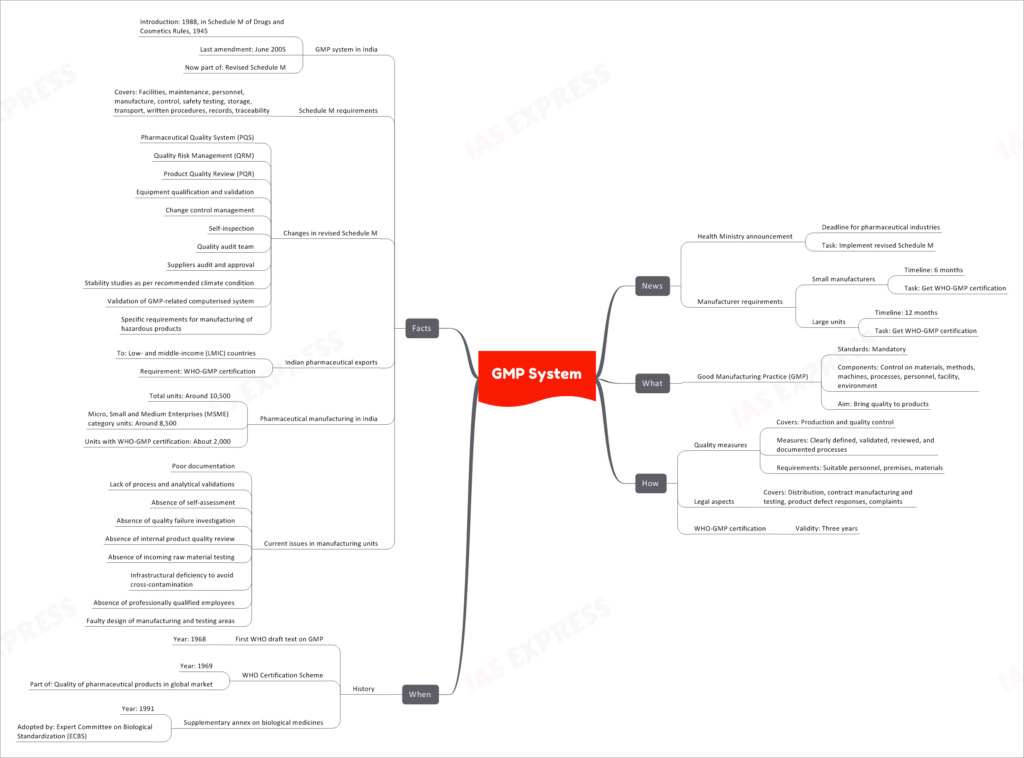
The Health Ministry has announced a deadline for pharmaceutical industries to implement the revised Schedule M, which focuses on Good Manufacturing Practice (GMP) standards. This move aims to bring quality to pharmaceutical products and improve manufacturing practices in India.
What is GMP?
Good Manufacturing Practice (GMP) is a set of mandatory standards that regulate various components of pharmaceutical manufacturing. It ensures control over materials, methods, machines, processes, personnel, facility, and environment, all with the ultimate goal of ensuring the quality of products.
How GMP is Implemented
GMP entails several measures to ensure quality in both production and quality control aspects of pharmaceutical manufacturing. These measures include:
- Clearly defining, validating, reviewing, and documenting processes.
- Meeting suitable personnel, premises, and material requirements.
- Addressing legal aspects such as distribution, contract manufacturing and testing, product defect responses, and complaints.
Pharmaceutical companies seeking compliance with GMP standards are required to obtain WHO-GMP certification, which remains valid for three years.
Historical Development of GMP
The concept of GMP dates back to 1968 when the first WHO draft text on GMP was introduced. The WHO Certification Scheme was established in 1969, and it became part of the broader effort to ensure the quality of pharmaceutical products in the global market. Subsequently, a supplementary annex on biological medicines was adopted in 1991 by the Expert Committee on Biological Standardization (ECBS).
GMP System in India
GMP was introduced in India in 1988 through Schedule M of the Drugs and Cosmetics Rules, 1945. The last amendment to this schedule was made in June 2005, and it is now part of the revised Schedule M.
The revised Schedule M includes several changes to enhance pharmaceutical quality and safety. Some of these changes include:
- Pharmaceutical Quality System (PQS)
- Quality Risk Management (QRM)
- Product Quality Review (PQR)
- Equipment qualification and validation
- Change control management
- Self-inspection
- Quality audit team
- Suppliers audit and approval
- Stability studies as per recommended climate condition
- Validation of GMP-related computerized systems
- Specific requirements for manufacturing hazardous products
Importance of GMP Certification for Indian Pharmaceutical Exports
For Indian pharmaceutical exports to low- and middle-income countries (LMIC), WHO-GMP certification is a crucial requirement. Among the approximately 10,500 pharmaceutical manufacturing units in India, around 8,500 are classified under the Micro, Small, and Medium Enterprises (MSME) category. However, only about 2,000 of these units currently possess WHO-GMP certification.
Current Issues in Manufacturing Units
Several challenges persist in the pharmaceutical manufacturing industry, including:
- Poor documentation
- Lack of process and analytical validations
- Absence of self-assessment and quality failure investigation
- Lack of internal product quality review
- Absence of incoming raw material testing
- Infrastructural deficiencies to avoid cross-contamination
- Lack of professionally qualified employees
- Faulty design of manufacturing and testing areas
Conclusion
GMP is a crucial regulatory framework that ensures the quality and safety of pharmaceutical products. The recent announcement by the Health Ministry to implement the revised Schedule M emphasizes the importance of compliance with GMP standards in India’s pharmaceutical industry. By addressing current issues and encouraging adherence to GMP, the country’s pharmaceutical sector can strengthen its position in the global market and provide safe and effective medicines to patients worldwide.
If you like this post, please share your feedback in the comments section below so that we will upload more posts like this.